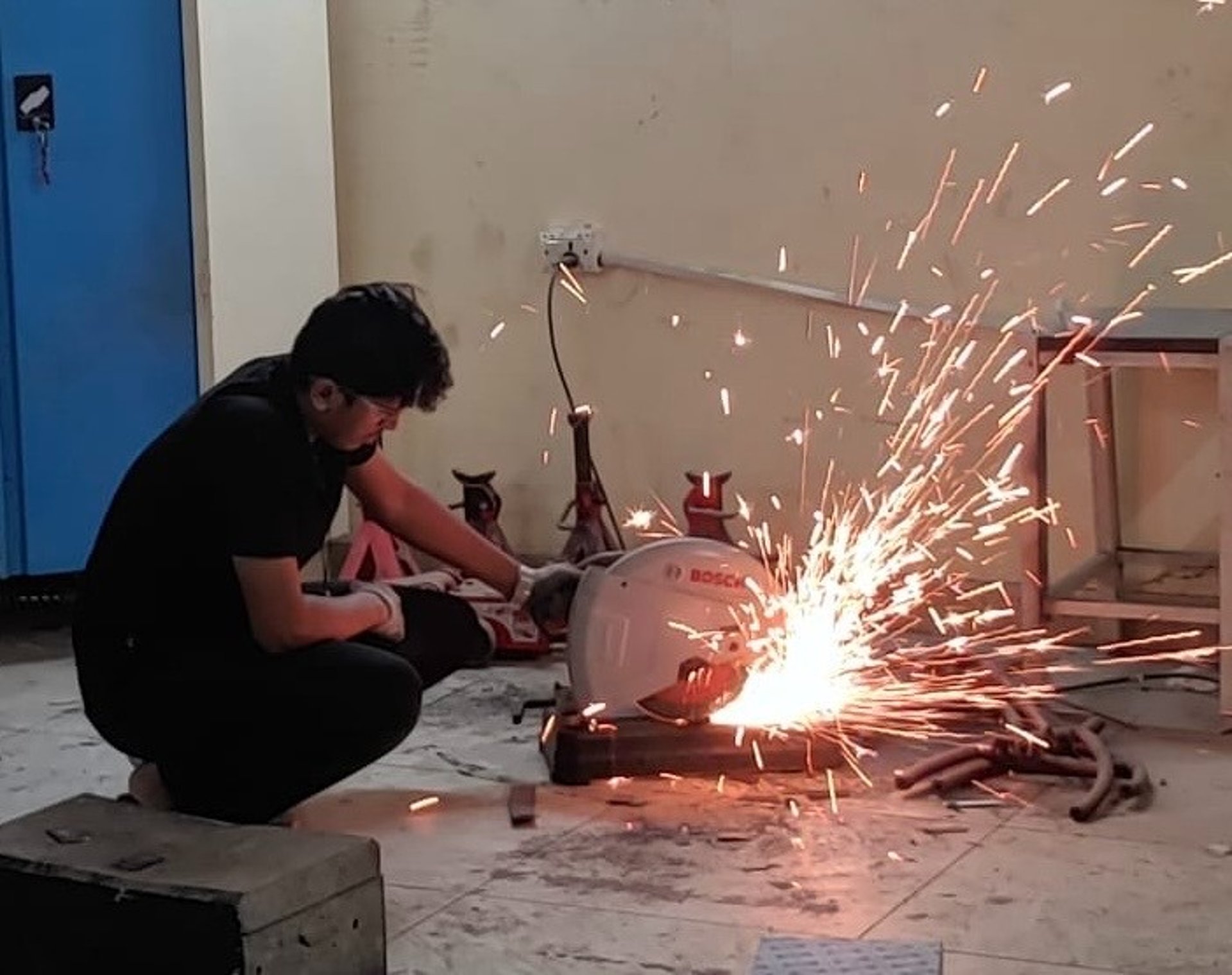
PROJECTS
Baby Panther - 4 Legged Robot
Dec 2024
What
Designed and developed a bio-inspired quadruped robot from scratch, capable of executing multiple gait patterns and specialized movements with precision and agility.
How
A detailed CAD model was then developed in Autodesk Fusion 360 to refine the structural and mechanical aspects of the robot. The components were fabricated using additive manufacturing and complemented by laser cuttings. A Raspberry Pi was utilized as the central processing unit, interfacing with servo motors and motor controllers to enable smooth and synchronized movements. Python scripts were developed to generate complex gaits, allowing the robot to perform various actions, including trotting, walking, bounding, handshake motions, and stable bipedal stances.
Results
The quadruped robot showcased high-speed locomotion of up to 35cm/sec with seamless transitions between gaits, demonstrating exceptional stability and control during all movements. The successful integration of advanced design techniques, manufacturing, and control systems resulted in a versatile and high-performance robotic system.
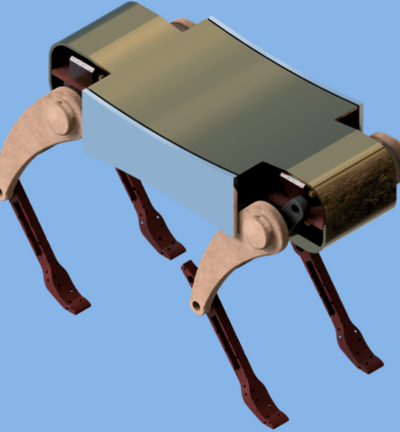
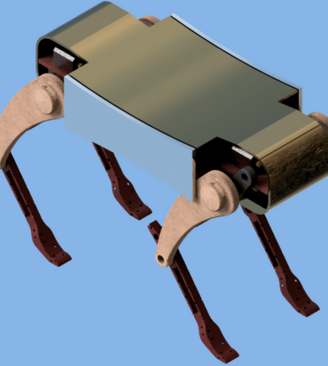
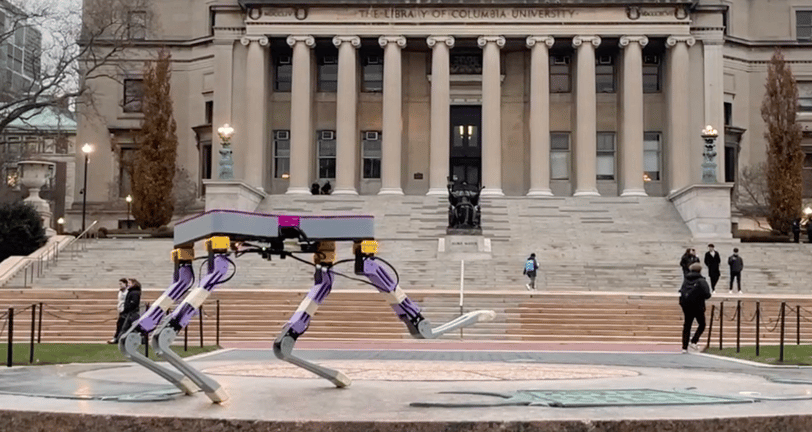
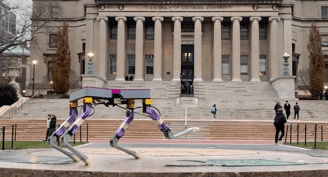
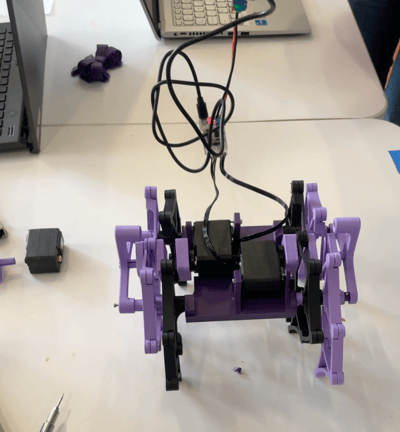
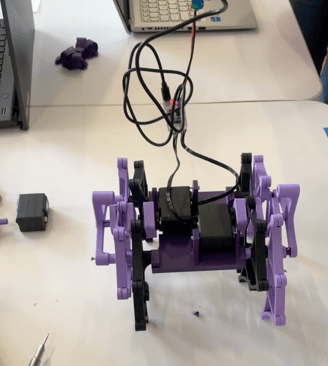
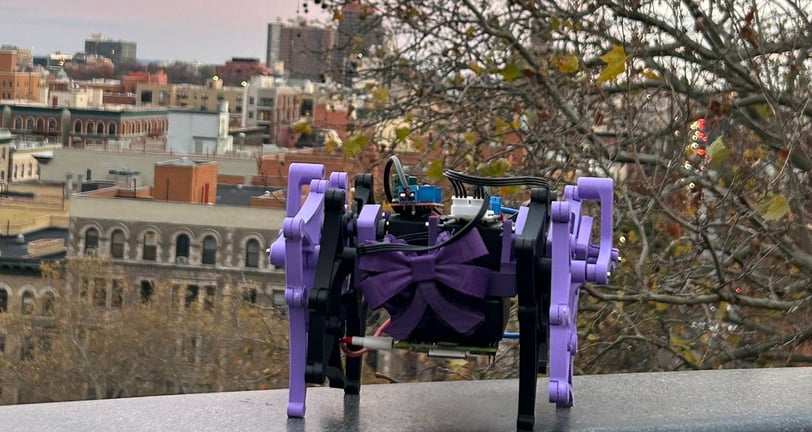
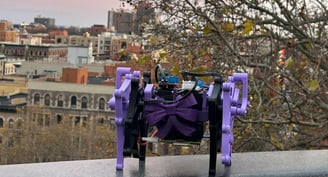
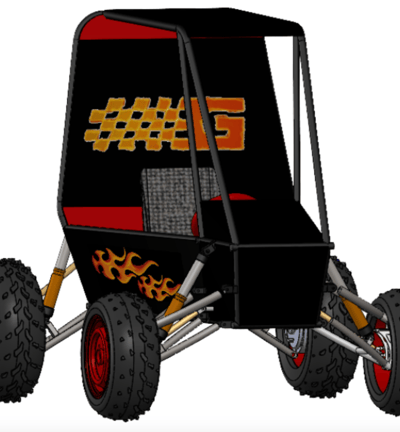
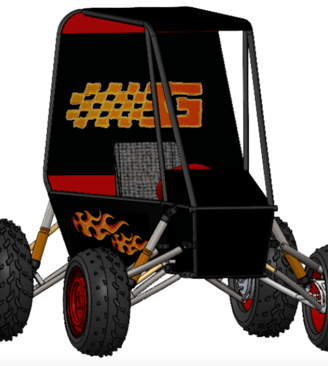
Bio-Inspired Spider Robot
Nov 2024
What
This project developed a spider-inspired walking robot leveraging the Theo Jansen mechanism, a bio-mimetic design that replicates smooth, natural locomotion. The robot is designed for versatile mobility, including forward and backward movement and turning, with intuitive control via WASD keyboard inputs.
How
The intricate geometries and joint configurations of the Theo Jansen mechanism posed significant manufacturing challenges. To overcome these, extensive 3D printing simulations were conducted to optimize printing parameters. This resulted in an innovative design where all joints are printed in place, eliminating the need for post-print assembly of individual legs.
Results
The streamlined manufacturing process reduced complexity and ensured precise joint articulation. The resulting robotic system demonstrates high efficiency and functionality, showcasing the effectiveness of the Theo Jansen mechanism in achieving fluid and versatile robotic locomotion.
Electric All Terrain Vehicle
June 2022
What
The Beast is a high-performance vehicle designed for all-terrain use with a focus on driver safety. It features rear-wheel drive (RWD) powered by two Brushless DC (BLDC) in-wheel hub motors, an optimized suspension system, a rack and pinion steering mechanism, and a front/rear split braking system. The vehicle is powered by Li-ion batteries, offering a top speed of 55 km/h, and emphasizes durability and driver ergonomics, especially through its roll cage design and safety features.
How
The design of the roll cage was iteratively developed using finite element analysis (FEA), material selection, and ergonomic considerations. AISI 4130 was chosen for its strength, and the frame was designed for driver comfort, incorporating optimal cockpit dimensions and seating angles. The steering system was designed with a rack and pinion mechanism, integrated through Python-based calculations to optimize steering geometry and precision handling. Suspension was optimized through iterative calculations to ensure both off-road capabilities and a smooth ride. The powertrain incorporates high-efficiency 48V BLDC motors with regenerative braking and a battery management system (BMS) for stable performance. Braking performance was ensured by calculating brake torque and clamping force, leading to an optimized braking system design.
Results
The Beast delivers high efficiency with an RWD configuration and a 91% efficiency BLDC motor, extending range to 1.2 hours of operation. The roll cage ensures driver safety, while the suspension and steering systems offer precise handling and comfort on all terrains. The braking system is optimized for safety and effective thermal dissipation. Together, these elements result in a high-performance, safe, and durable vehicle suitable for varied terrains and driving conditions.
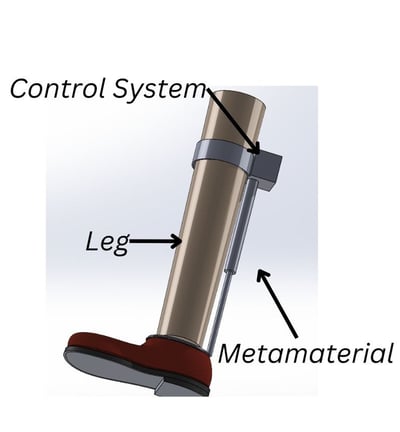
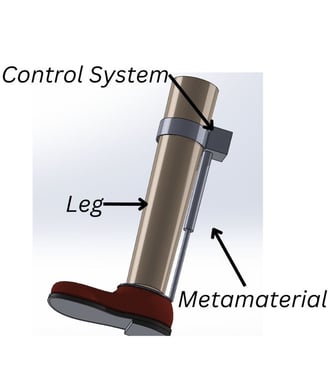
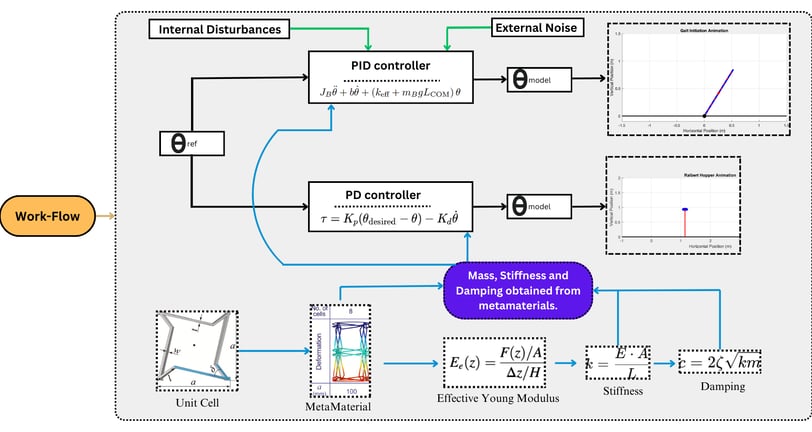
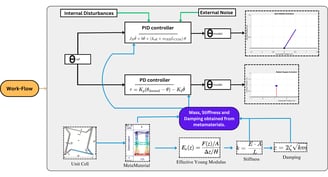
Material-Driven Innovations for Locomotion
Dec 2024
What
This work introduces a novel approach to dynamic locomotion, utilizing metamaterial-based leg designs integrated with optimized control strategies. These legs replace conventional spring-damper systems by offering intrinsic stiffness and damping, enabling energy-efficient and robust motion.
How
The research uses two computational models to study and optimize locomotion in Parkinson's Disease (PD) patients. The Inverted Pendulum Model simulates impaired anticipatory postural adjustments (APAs) in gait initiation, employing a PID controller to stabilize and improve gait. The Dynamic Raibert Hopper, based on the SLIP framework, integrates PD control and neuromechanical insights to analyze the effects of reduced dorsiflexor activation on stability and energy-efficient gait. These models provide a comprehensive understanding of locomotor dynamics and inform therapeutic strategies for PD.
Results
The metamaterial legs, coupled with the optimized control strategies, achieved performance on par with traditional actuators, delivering improved energy efficiency, robustness, and system simplicity. This innovation has potential applications in rehabilitation robotics, bio-inspired systems, and dynamic locomotion research, contributing to the development of advanced, material-driven robotic systems.
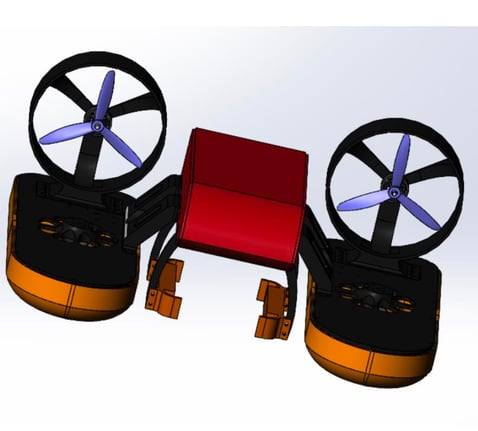
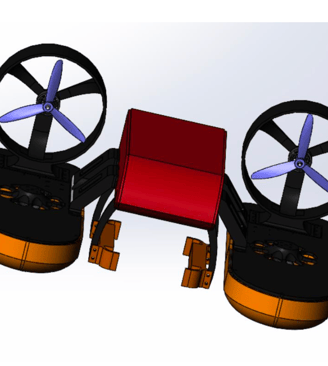
Hovercraft Resupply Vehicle Design
April 2023
What
The objective of the project was to design and manufacture a hovercraft only using additive manufacturing that could pick up and carry a payload through a ground course, delivering it to its final destination.
How
The team used an iterative design process, ensuring physical results aligned with simulations. A key innovation was a TPU-printed skirt with PETG-CF inserts and a detachable base for easy replacement. Neodymium magnets and GI sheet pieces were embedded for improved functionality.
The "GyroCompressible Pad" was created for the payload mechanism, using TPU and PETG Carbon Fiber for load-bearing parts. PLA was used for the housing and base plate. The hovercraft featured four BLDC motors for thrust and hover, with steering controlled by motor speed variation. The main circuit was built on a perfboard with Arduino Nano, MPU6060, and Flysky i6. Digimat-AM was used for numerical analysis of component stresses.
Results
Through multiple iterations and testing, the hovercraft design successfully integrated innovative 3D-printed components and modular systems, achieving enhanced performance and ease of maintenance. The design was optimized for maximum functionality and durability, enabling the hovercraft to carry out its payload transport tasks effectively. The final design demonstrated solid performance, with well-coordinated motor control for both hovering and steering.
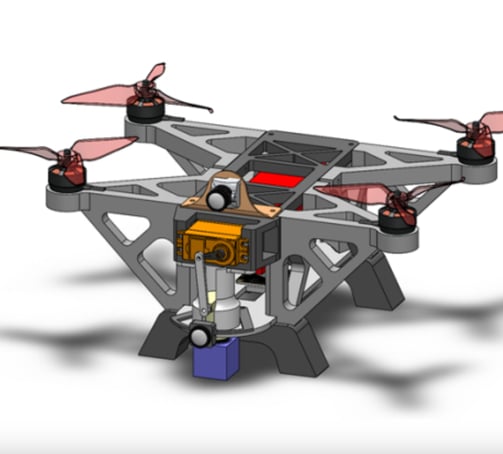
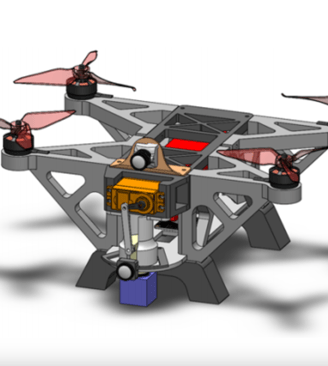
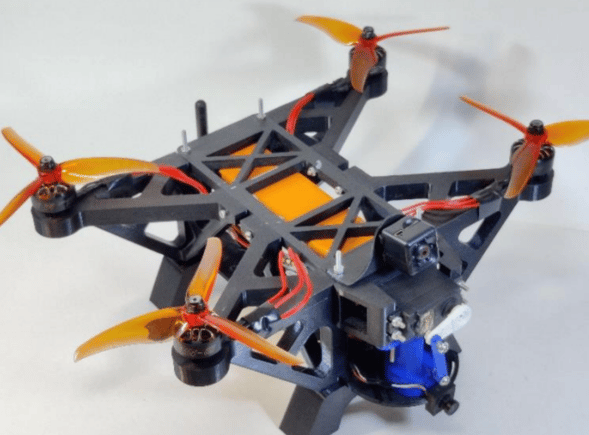
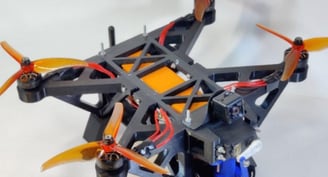
Unmanned Aerial Vehicle
April 2021
What
The objective was to create a Unmanned Aerial Racing Cargo Vehicle capable of picking up and dropping a payload while completing five laps on a racecourse
How
The quadcopter was fabricated using PETG with Fused Deposition Modeling (FDM). A servo-powered slider-crank mechanism enabled payload pick-and-drop without landing. Embedding the li-po battery within the airframe and using uniquely designed arms improved stability and stress distribution. SolidWorks aided design and simulation, while Cura slicer optimized the model for 3D printing. The center of mass was aligned near the geometric center for enhanced stability and agility. An FPV system and F7 flight controller ensured responsive navigation, and a 4S 5200 mAh battery delivered 11 minutes of flight time, balancing weight and endurance.
Results
Extensive prototyping and testing led to a design solution that met the competition's objectives, resulting in a stable, agile, and effective vehicle. The UARCV showed significant improvements over the previous year's design, successfully demonstrating its capabilities in payload handling and racecourse traversal.
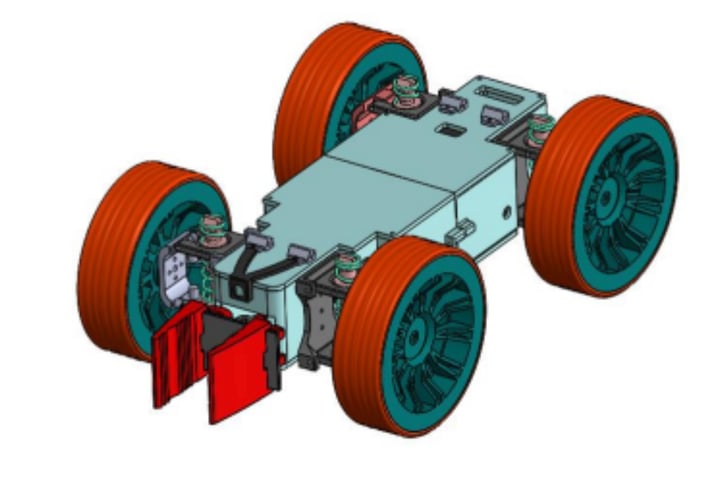
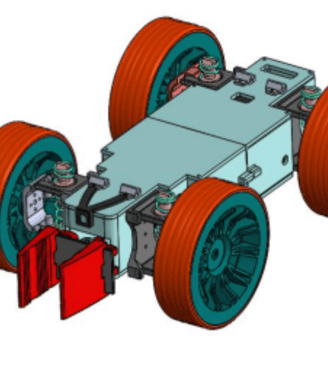
Ground-Based Remote-Controlled Vehicle
April 2022
What
The goal of this project was to design, test, and manufacture a Ground-Based Remote-Controlled Vehicle (GBRCV) using additive manufacturing. The vehicle was engineered to perform a variety of tasks, including environmental navigation, freestyle tricks, long jumps, high-speed performance, precise cornering, and gripping.
How
An iterative design process enhanced efficiency and innovation. Sharp turns were enabled by an Ackermann-based bell crank mechanism. The bot’s modular, symmetrical design allowed operation when flipped, with a 45:55 weight distribution optimizing stability.
The design minimized parts and simplified assembly. A servo-powered gripper handled varied objects, while TPU wheel covers absorbed impacts. Navigation used an FPV system, with four in-hub motors controlled by Arduino Uno. A 4S battery powered all components. SolidWorks and Ansys ensured a safety factor above 1.5 before testing.
Results
The iterative prototyping and testing process resulted in a finely tuned GBRCV capable of excelling in the outlined performance objectives. The vehicle demonstrated excellent cornering precision, stability during acceleration and deceleration, and effective gripping capabilities. The modular and symmetrical design proved robust, while the use of additive manufacturing optimized part durability and assembly.
7
6
5
4
3
2
1
8
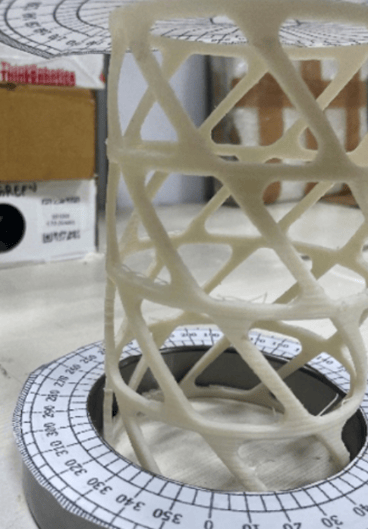
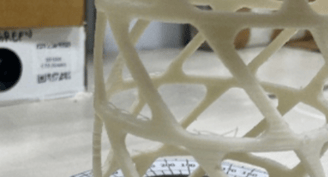
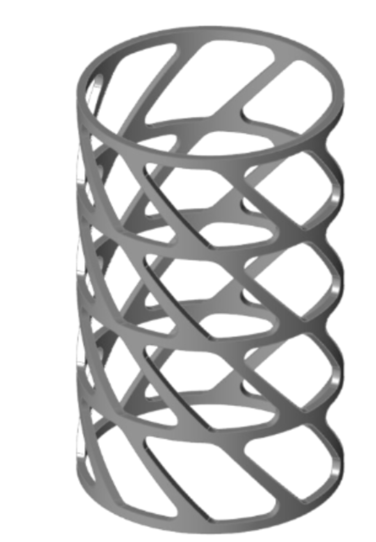
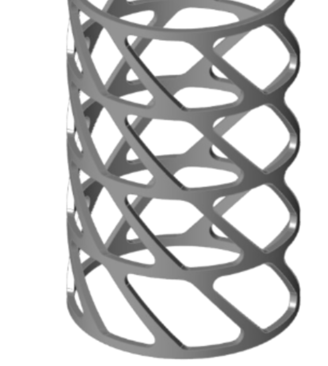
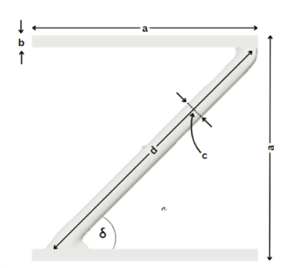
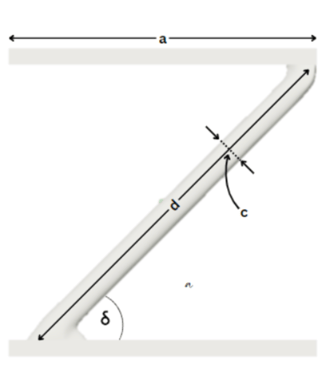
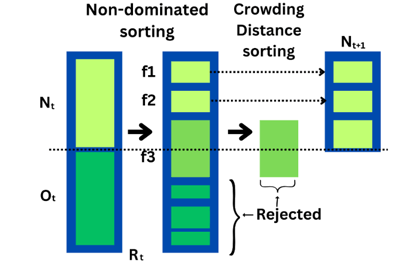
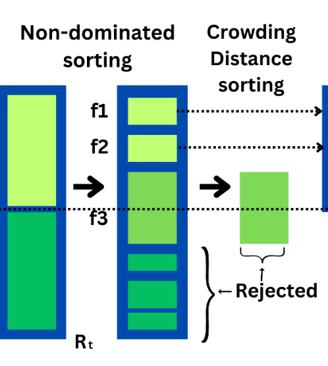
Hip Joint Structural Optimization
July 2023
What
A novel Compression Torsion Conversion Metamaterial (CTCM) was developed using advanced structural optimization techniques like generative design and topology optimization and additive manufacturing.
How
The study employed Solid Isotropic Material Penalization and Non-Dominated Sorting Genetic Algorithm II for structural optimization, ensuring high-performance designs. A comprehensive parametric study was conducted to evaluate the influence of various parameters on torsion conversion capabilities. The CTCMs were fabricated using additive manufacturing, with simulations determining the most optimal process parameters for enhanced print quality.
Results
The developed CTCMs exhibited exceptional properties, achieving a torsion conversion of 38° at 7% strain, outperforming other similar materials in the literature. The numerical and experimental analyses showed strong correlation, validating the optimized models. These results highlighted the superiority of the CTCMs in terms of torsion conversion capabilities and reduced weight.
9
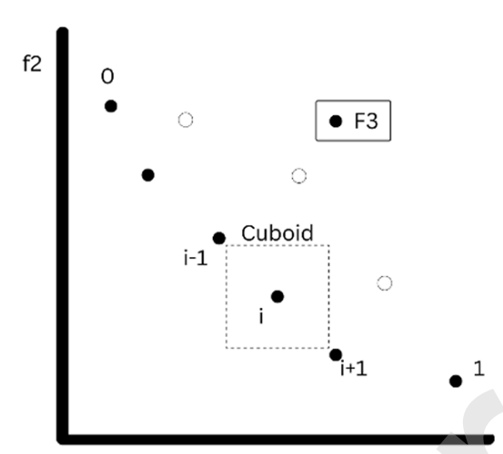
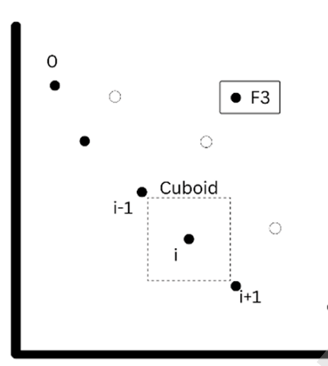
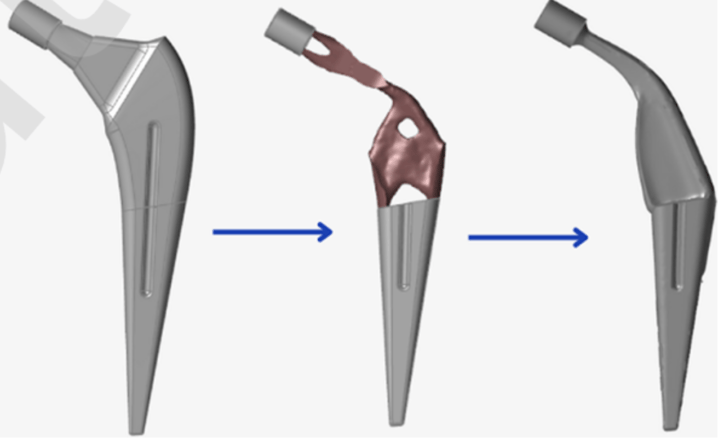
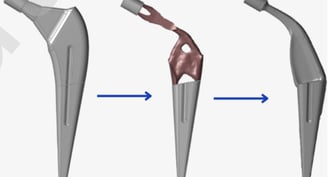
Compression Torsion Conversion Metamaterials (CTCM)
Jan 2024
What
This paper investigates the design and analysis of Ti-6Al-4V hip joint implants using generative design, topology optimization, and laser powder bed fusion (LPBF), an additive manufacturing technique.
How
The study utilized the NSGA-II genetic algorithm and the solid isotropic material penalization approach. This combined approach effectively reduced the implant mass by up to 75% while preserving structural integrity. Finite element analysis revealed that the combined method of applying topology optimization followed by generative design achieved a 40% reduction in deformation and a 15% reduction in von Mises stress compared to conventional models.
Results
The optimized Ti-6Al-4V hip joint implant designs demonstrated superior mechanical performance and manufacturability. The combined approach of topology optimization and generative design led to reduced stress and deformation while achieving significant mass reduction.
Contact
New York City, New York, USA
+16462840393
abhishek.kishor@columbia.edu